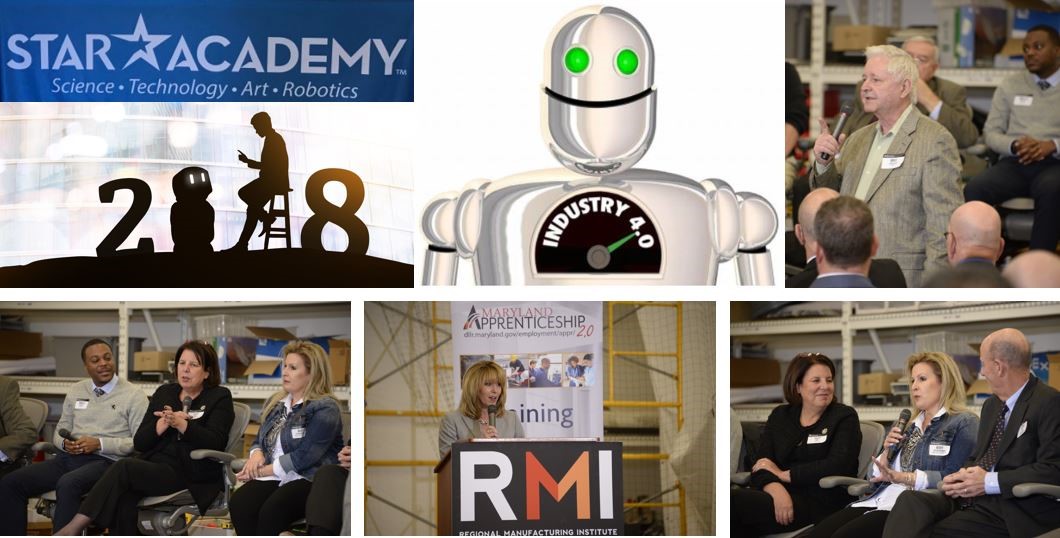
(from top right, Mike Galiazzo of RMI; left-to-right Suzy Ganz of Lion Brothers: DLLR Secretary Kelly Schulz; Mary Steinbrunner of Dunlop Boots)
On January 17, the Regional Manufacturing Institute (RMI) brought together a cross-section of Maryland business, government and academic thought leaders to discuss, with an audience of 200, the impact of “industry 4.0” on Maryland Manufacturing. Industry 4.0 is the term used to describe the Fourth Industrial Revolution, a new period in history marked by digitization and advanced technologies (Google Industry 4.0). Thought leaders included: Aris Melissaratos, Dean, Brown School of Business and Leadership, Stevenson University; Suzy Ganz, Chairman and CEO, Lion Brothers; David Eschbach, Senior Project Leader- Smart Factory, Stanley Black & Decker; Mary Steinebrunner, General Manager, Dunlop Protective Footwear USA; George Davis, CEO, TEDCO; Adam Porter, Director, Fraunhofer USA – 4.0 and W. Donald Walker III, Branch Manager, Baltimore Kelly Services.
Industry 4.0 tools allow companies to use data and analytical tools to help drive decision making. The impact is real as companies are reporting significant increases productivity through various real-time data feedback loops. Adopters of digitization report that data are now being shared in a cross-functional way allowing executives to have a 360-degree view of their operation based on analytical data previously unavailable.
“Industry 4.0 principles, practices and technologies will transform Maryland manufacturing into a national showcase of next-generation manufacturing unequaled in stature and global competitiveness,” said Dr. Mike Galiazzo, President of RMI. Maryland manufacturers are keen to find out what they need to do and where they need to start.
Over the past year, RMI has been leading an Industry 4.0 initiative, acting as a convener for Maryland manufacturing companies to share their thoughts on the value of becoming more digitally-integrated. The January 17 program provided some excellent examples of companies attaining very tangible and measurable impacts on their productivity and innovation. The forum also helped gauge their adoption of many of the new 4.0 technologies in their workplace and what kinds of resources they require to continue their journey.
Several manufacturers are showing the way to 4.0 through their respective journeys including Lion Brothers, Dunlop Boots, and Stanley Black & Decker. With the Star Academy in Timonium as the backdrop with its showcase of robots, drones and virtual reality equipment, some of Maryland’s top visionaries gave their insights on the digitization movement.
“The Industry 4.0 adoption for Lion Brothers was a 180-degree journey which has focused on employees of all ages and experience levels, from millennial to veteran employees and looking at new ways of doing things,” said Suzy Ganz, Chairman and CEO of Lion Brothers in Reisterstown, Maryland. “Our success to date reflects an integration and amalgamation of our smart talent and all of their ideas,” she said. Lion has been on the digitization journey which took them from threading looms to create patches in the early years, to today where they have become the leading designer and manufacturer of apparel brand identity systems using the latest digital technologies for manufacturing and customization. “Last year we grew our revenues by 55%, and we now have margins more like a tech company as opposed to a legacy company,” she said.
Corporate culture is a big topic when it comes to revamping operations from analog to digital. Kelly M. Schulz, Secretary of the Maryland Department of Labor, Licensing and Regulation, reacted to the comments she heard from companies pondering what it will take attract younger “industry 4.0 talent” to adopt new technologies and the digital transition. “Career pathways help attract and retain top talent and are especially important to manufacturers making the 4.0 transition,” she said. “Today’s young employees want to work in digital environments with new technologies, where they can receive training, grow, and advance in their career. Hiring registered apprentices and training incumbent workers through Maryland’s EARN program are proven strategies that deliver the kind of direction and support today’s workers seek.”
At Dunlop Protective Footwear USA in Havre de Grace, Mary Steinebrunner, the company’s General Manager is a big advocate for digitization. “Rather than competing with China on a $10 boot; we’re now knocking it out of the park with a $150 boot, providing a better boot with increased protection and one that people want to wear for a variety of purposes,” she said. “For years we were stuck in a flat sales cycle, but due to our 4.0 journey enabling the evolution of our product offering, we’ve started the upward tick and will double our sales growth in the next three years.”
“This 4.0 journey is a lot of work, but we want to double our employee base from our current 103, and every single topic that is discussed, people and tech play such an important part. “We used to hire a person for a job; now we’re showing them a forward path that is exciting, a more cross-functional role,” she said. “It’s key to retaining our employees.”